Fabricación Bio Diesel
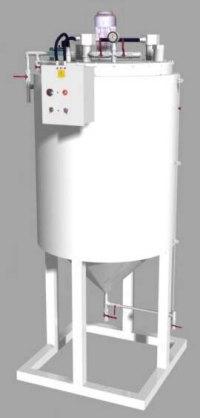
Bio Diesel
El costo del biodiesel será esencialmente el costo del aceite; suponiendo que el costo del aceite fuera de 0.35 el litro, el costo del biodiesel elaborado con dicho aceite será de 0.33/0.37 el litro.
Si uno muele grano propio, o grano comprado, el costo del aceite se abarata; de allí la importancia de integrar la extracción de aceite a todo proyecto de elaboración de biodiesel.
La BIO200 cuesta u$s 1750, ex-works; la BIO400 cuesta u$s 3300, ex-works. la garantia es de un año, materiales y mano de obra. el plazo de entrega es de 30 dias.
Una planta integrada que incluya una BIO400, una mini-planta para extraccion de aceite, depositos, e infraestructura, requerira una inversion de u$s 12.000, para una capacidad de 200.000 litros/año de biodiesel.
Consúltenos por la compra de este equipamiento o para la instalación y/o planos constructivos en el exterior de Argentina!!!!!
Precios a Abril de 2.001…
El Biodiesel como combustible alternativo
El combustible renovable que reemplaza al gasoil fósil se conoce como «BIODIESEL». Se elabora a partir de cualquier aceite vegetal. Su energía específica es un 5% menor que la del gasoil, pero su elevada lubricidad compensa esta diferencia; de allí que el rendimiento energético de ambos combustibles es esencialmente el mismo. Puede usarse puro, o mezclado en cualquier proporción con gasoil. No requiere modificación alguna de los motores. La lubricidad del biodiesel es notable; duplica la vida útil de los motores. Por esto se lo agrega al gasoil de bajo tenor de azufre para mejorar su lubricidad. También mejora el índice de cetanos del gasoil.
La fabricación de biodiesel es sencilla, y no requiere de economías de escala: Se parte de un aceite vegetal que se somete a un proceso de transesterificación. Como resultante de esto se obtienen biodiesel, y glicerol. Este último se utiliza como jabon, como desengrasante, o como base para la obtención de la glicerina. La transesterificación se logra mezclando el aceite vegetal con un alcohol y un álcali. Al cabo de un tiempo de reposo, se separan por decantación el biodiesel, y el glicerol. El biodiesel que se obtiene solo requiere filtrado para su uso. No se degrada con el tiempo, pudiendo almacenarse de idéntica manera que el gasoil.
El biodiesel reduce la contaminación. Las emisiones netas de dióxido de carbono (CO2) y de dióxido sulfuroso (SO2) se reducen un 100 %. La emisión de hollín se reduce un 40-60%, y las de hidrocarburos (HC) un 10-50 %. La emisión de monóxido de carbono (CO) se reduce un 10-50%. Se reduce igualmente la emisión de hidrocarburos policíclicos aromáticos (PAHs), y en particular de los siguientes derivados, de comprobada acción cancerígena: Fenantrén – 97%; Benzoflúorantren – 56%; Benzopirenos – 71%. Finalmente, la emisión de compuestos aromáticos y aldehídos se reduce un 13%, y las de óxidos nitrosos (NOx) se reducen, o aumentan, 5-10% de acuerdo con el desgaste del motor, y la calibración de la bomba inyectora.
El biodiesel es 100% biodegradable, y su toxicidad es inferior a la de la sal de mesa. Su combustión genera, de acuerdo al aceite vegetal que se utilice, un olor similar al de las galletas dulces, o al de las papas fritas. Los litros de biodiesel por hectárea que se obtengan dependerán del cultivo que dé origen al aceite vegetal. Los ejemplos a continuación dan una idea del potencial de cada cultivo.
- Soja (Glicine max): 420 litros
- Arroz (Oriza sativa): 770 litros
- Tung (Aleurites fordii): 880 litros
- Girasol (Helianthus annuus): 890 litros
- Maní (Arachis hipogaea): 990 litros
- Colza (Brassica napus): 1100 litros
- Ricino (Ricinus communis): 1320 litros
- Jatropa (Jatropha curcas): 1590 litros.
- Aguacate (Persea americana): 2460 litros
- Coco (Cocos nucifera): 2510 litros
- Cocotero (Acrocomia aculeata): 4200 litros
- ;alma (Elaeis guineensis): 5550 litros
El alcohol se utiliza en una proporción del 15 al 25%, y el álcali es menos del 1% del volumen. El alcohol exedente residual es recuperable. El glicerol que se obtiene puede venderse tal cual, transformarse en otros productos de mayor valor agregado, ó puede ser refinado para obtener glicerina. La venta del glicerol generalmente cubre el costo del alcohol, álcali, la electricidad, y la mano de obra. La reducción de los costos de producción del agro pasan forzosamente por la reducción del costo del combustible. El biodiesel, elaborado con insumos de origen local, abarata el combustible y prolonga la vida útil de los motores.
El biodiesel no requiere de megaproyectos, o inversiones avaladas por el Estado que impliquen honerosos créditos. De hecho, se puede hacer biodiesel con solo mezclar los componentes en una licuadora de uso doméstico. La adopción del biodiesel como combustible alternativo solo requiere la diseminación de la tecnología de proceso, y la toma de decisiones políticas que permitan distanciar a los poderosos intereses económicos y de prestigio que están en juego. A la industria petrolera no le agrada ser desplazada de sus mercados, y al sector académico no le placen las ideas generadas fuera de su ámbito. Esto hace que en aquellos países que mas lo necesitan, el biodiesel no prospere aún como alternativa
A medida que se popularice el uso del biodiesel, la humanidad descubrirá que puede generar la energía que necesita, al tiempo que logra un mayor valor agregado para su producción primaria, y mejora el ambiente en que vive. Y esto hará del biodiesel, antes que un combustible, una puerta hacia la libertad.
Reactores Bio200 y Bio400 para elaboración de biodiesel
A) ANTECEDENTES
La transesterificación de los aceites vegetales mediante alcoholisis permite obtener GLICEROL, y alcoholester de ácido graso, comunmente denominado BIODIESEL. Los reactores BIO han sido diseñados con la finalidad específica de transesterificar aceites vegetales en forma sencilla y a bajo costo, tanto operativo como de inversión. Para ello hacen uso del proceso base/base, mejorado gracias a la alta temperatura y presion de proceso, y a la incorporacion de un mezclador/agitador de alta velocidad.
B) DESCRIPCIÓN
Los reactores BIO son presurizados, con calefacción eléctrica, y utilizan tecnologia de agitado/mezclado de alta velocidad. Estan dotados de aislación de poliuretano expandido, y regulación automática de presión y temperatura de proceso. La construcción es en acero SAE1010, con revestimiento epoxy. Los elementos utilizados son de facil obtención en todo el mundo; la filosofia de diseño fue la de adoptar criterios universales en cuanto a materiales y componentes. La construcción cumple con las normas DIN y ASTM para seguridad industrial, y ambiental. Las plantas BIO no generan efluentes. Estan venteadas para evacuar los vapores de alcohol que pudieran generarse durante el llenado. El venteo se utiliza igualmente para el recupero opcional del excedente de alcohol. El tablero de control es estanco; los circuitos eléctricos estan entubados. Todos los circuitos eléctricos tienen protección propia adicional a la protección general del tablero. Se provee un plano detallado de los circuitos eléctricos.
C) COMPONENTES E INSTRUMENTACIÓN
El circuito de llenado esta provisto de dos entradas independientes que se contectan a la provisión de alcohol y aceite, y de una electroválvula que se comanda desde el tablero. El nivel de llenado es controlado visualmente. El concentrado de álcali/alcohol se introduce por una boca independiente, lo que permite el prefiltrado del mismo. La temperatura de reacción se regula desde el tablero; para ello se proveen un termóstato y un termómetro análogo para control. Los controles de temperatura son de tipo capilar, lo que asegura la confiabilidad de los mismos. La presión de reacción se fija mediante un regulador incorporado en el circuito de aire comprimido. Se incluye un manómetro analogo para control, y válvula de seguridad.
D) OPERACIÓN
Se incorpora el alcohol, y se inicia la agitación/mezclado. A continuación se vierte el concentrado álcali/alcohol. Finalmente se incorpora el aceite. Se cierra el venteo y se presuriza la planta al mismo tiempo que se habilita el circuito de calefacción. Cuando se completa el agitado/mezclado, se desactiva el circuito de calefacción, y manteniendo la presión se espera el tiempo necesario para que ocurra la separación por decantación del glicerol y el biodiesel. Se extrae el glicerol aprovechando la presión en el reactor, y a continuación se extrae el biodiesel, que es filtrando a cinco micrones. El biodiesel que asi se obtiene esta listo para ser usado o almacenado.